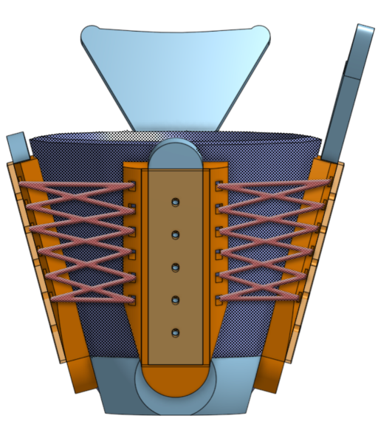
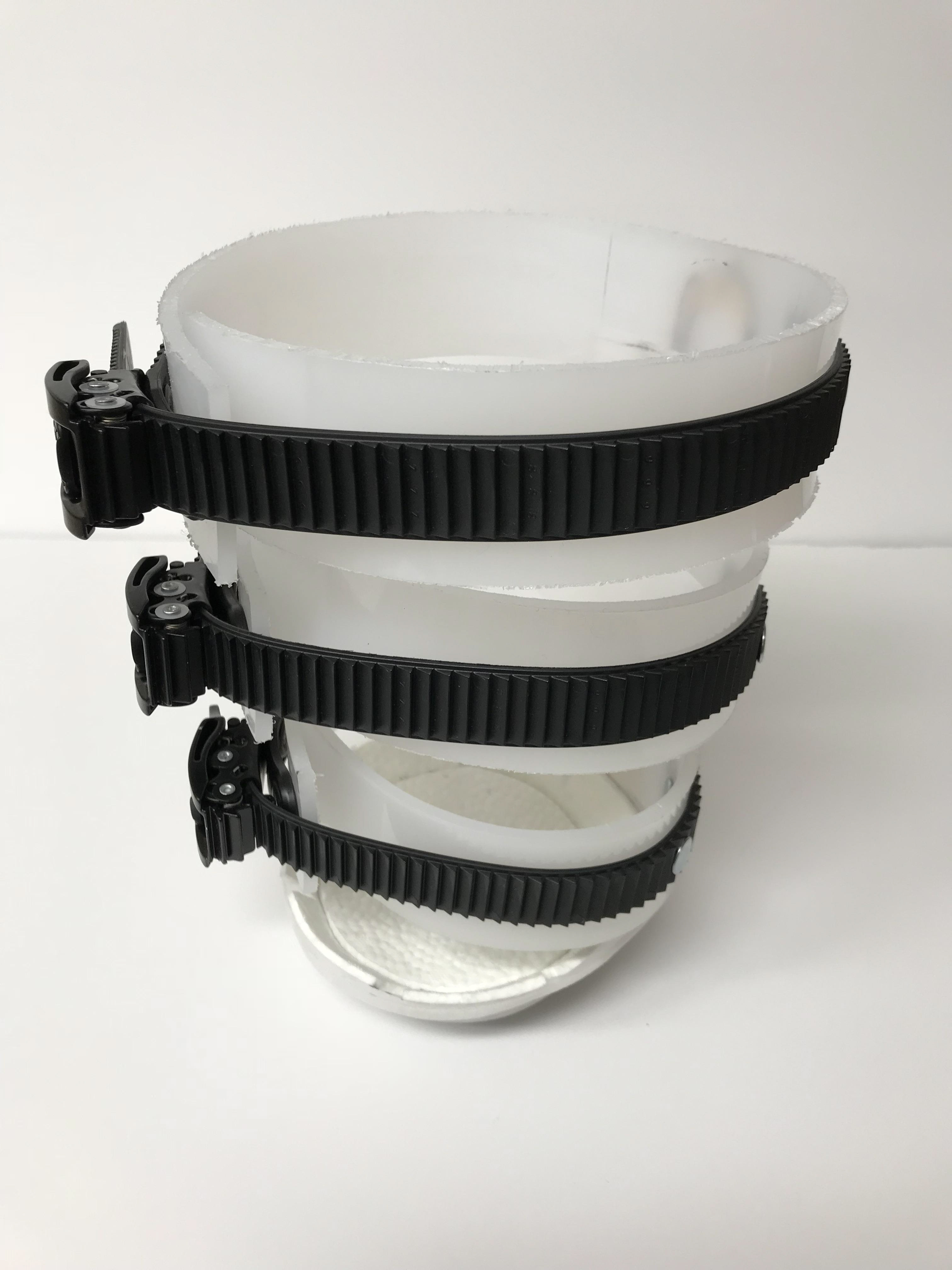
Recognitions: Doris M. and Norman T. Halpin Prize; Brown Hack Health; George H. Main Award
Articles: https://news.brown.edu/articles/2018/09/b-lab
https://brunonia.brown.edu/giving/article/enabling-disabled-affordable-prosthetic-design
Based on our success at the Brown Hack Health, we decided to continue our project for our Biomedical Engineering Capstone project, and make it our focus for Koi Prosthetics. Through our trip to Vietnam and feedback from local prosthetists, we learned that a bottleneck to prosthetic accessibility is due to the socket fitting process. It takes weeks to fit a traditional custom-fitted socket; most amputees cannot afford to be travelling back and forth, while hospitals have to go through customized materials. We wanted to create a "one-stop shop" prosthetic socket for transfemoral amputees. Above-knee amputations are most common in developing countries due to poor infrastructure, lack of healthcare access, and war. According to the World Health Organization, there are almost 40 million amputees in developing countries, and only 5% have access to prosthetics. Our goal was to create a design that allowed the user to adjust the socket to their residual limb size-- both width and length-- and not need a specialist for fitting.
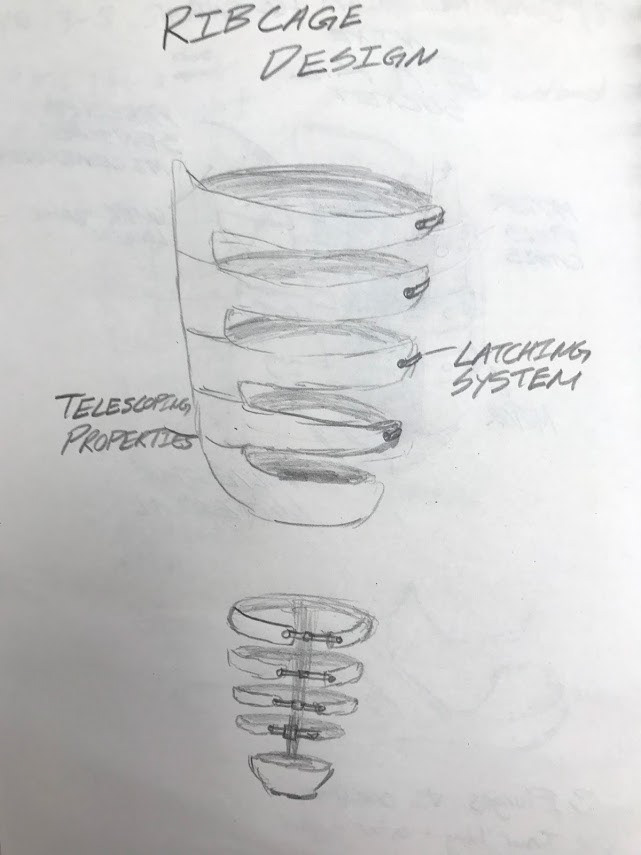
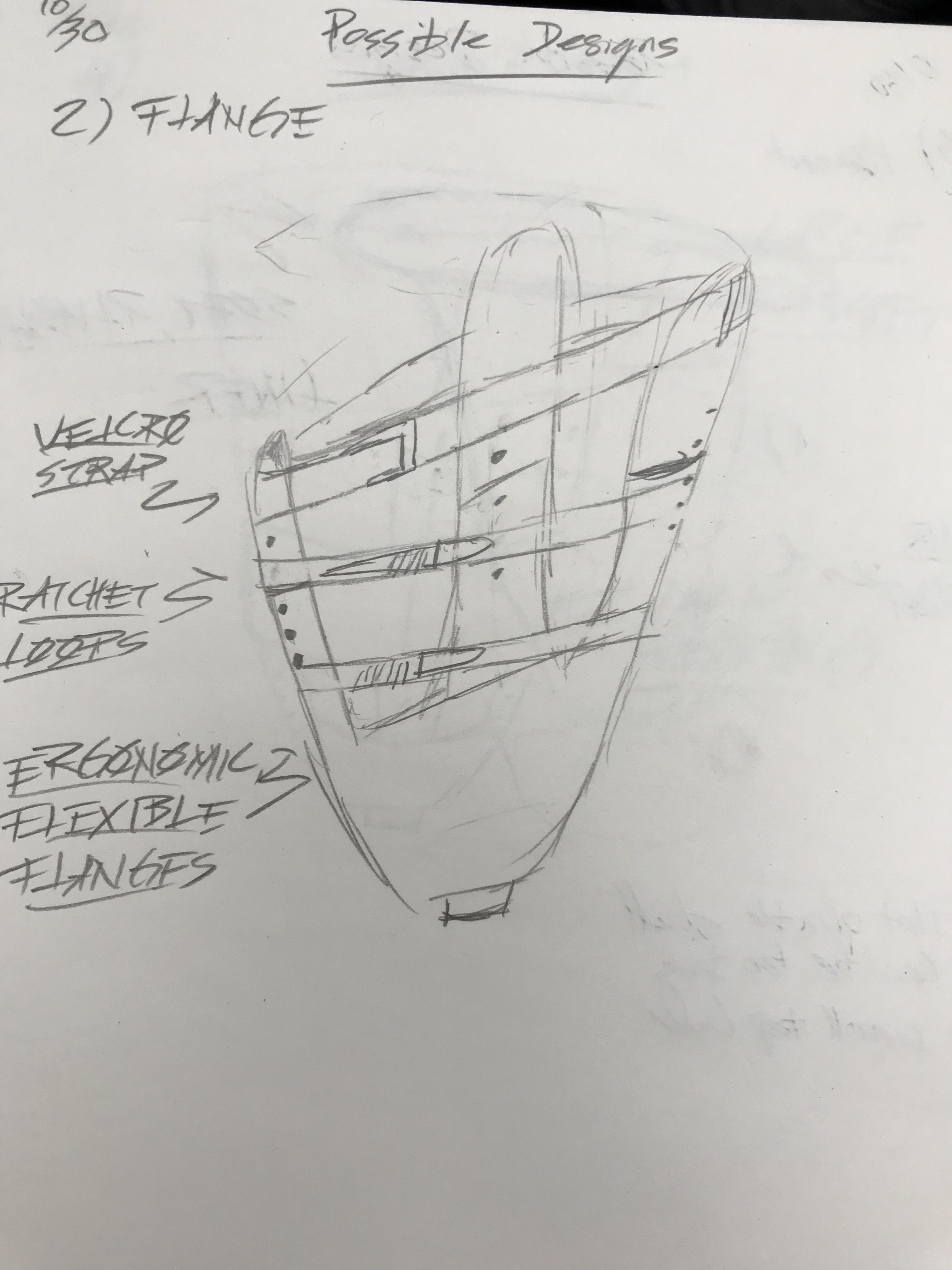
Both designs were novel, but the tripod design shared similarities to an existing socket. In addition, we had created the tripod design in Brown Hack Health, so we wanted to explore something different. We were advised by local prosthetics, orthopedic doctors and clinics. The socket is a "volume holder"; the bottom cup withstands forces while the rest holds the residual limb comfortably in place. Based on our research and mechanisms, we created the Ribcage design.
We first created a "looks-like" model out of cardboard to get an understanding of how the mechanisms would interact with each other. We wanted easy width adjustment and sturdy length adjustment; so we tried out different mechanisms that would work. We realized we needed more modularity and create a way to keep the centers of each flange aligned. We also learned that the flanges needed to be different lengths
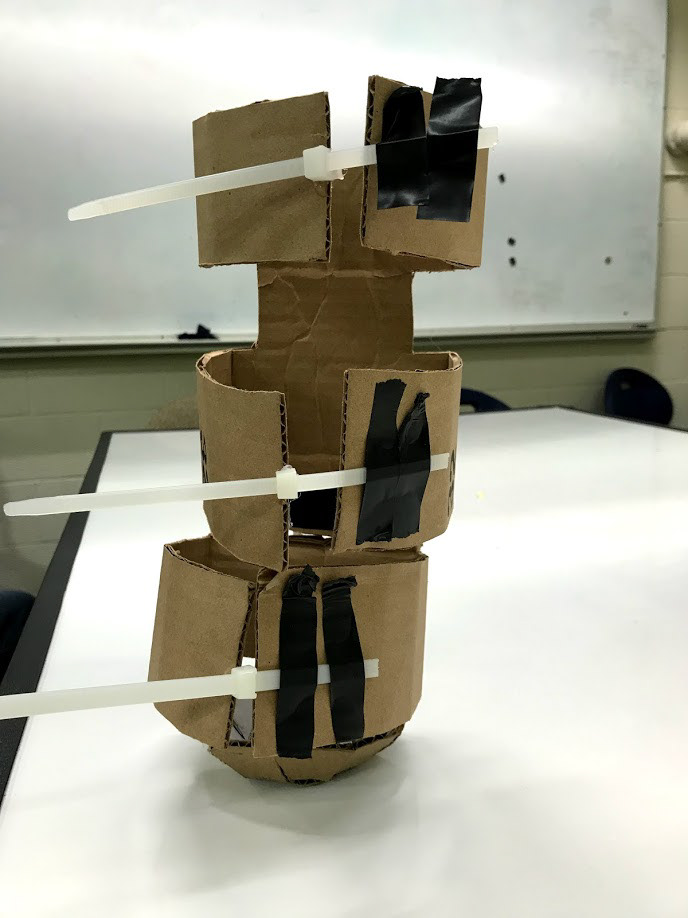
From there, we created a "works-like" model. Using extruded polypropylene and velcro, a second iteration was created. It molded using heat guns and conformed to the shape of residual limb molds. In addition, we ran orthogonal design to determine the best overall material. We ran heating tests to decide which material was sturdy, yet easy to work with. We did not have access to an oven, so we had to carefully heat mold the socket.
Through experiments, we decided to create our "final" prototype out of Low Density Polyethylene. We ran stress analysis on the material and design to show that it would hypothetically work while a person used it.
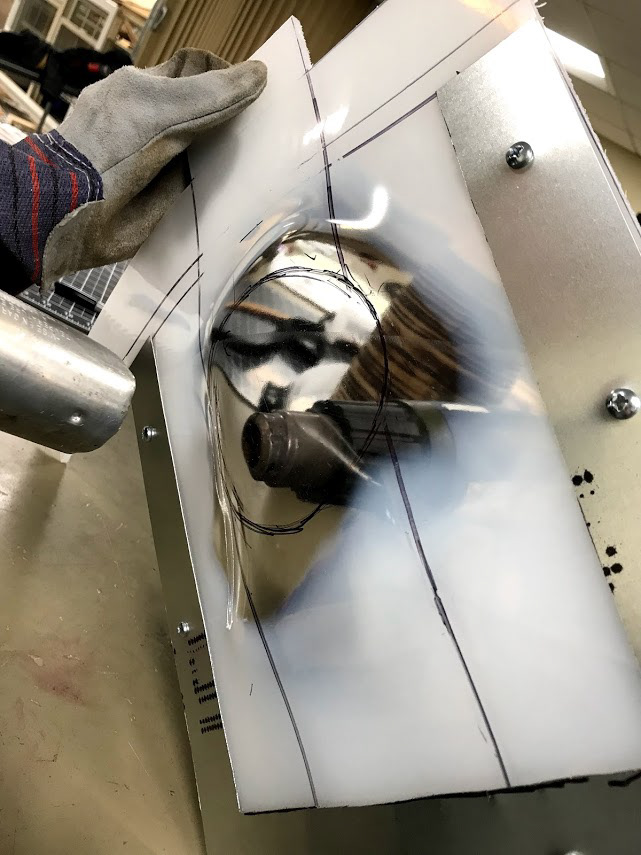
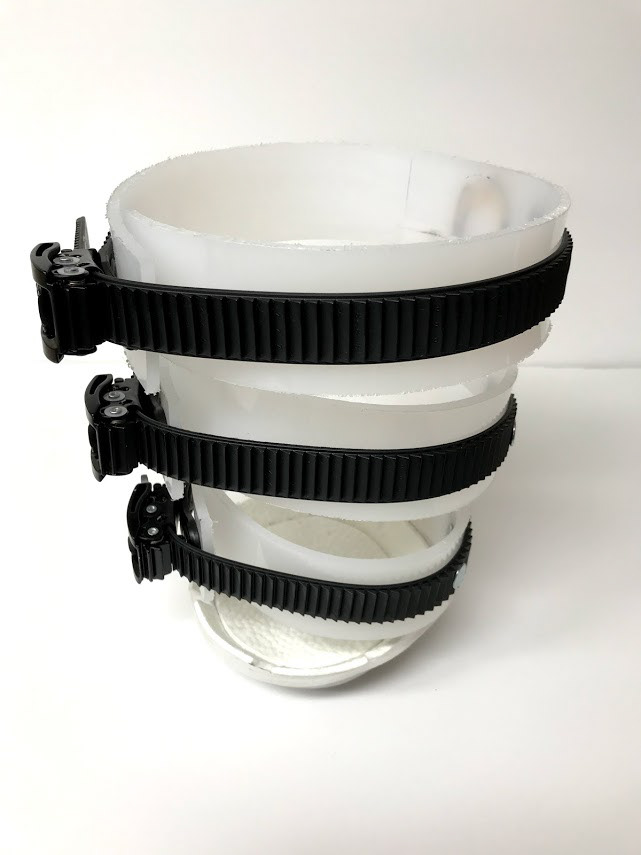
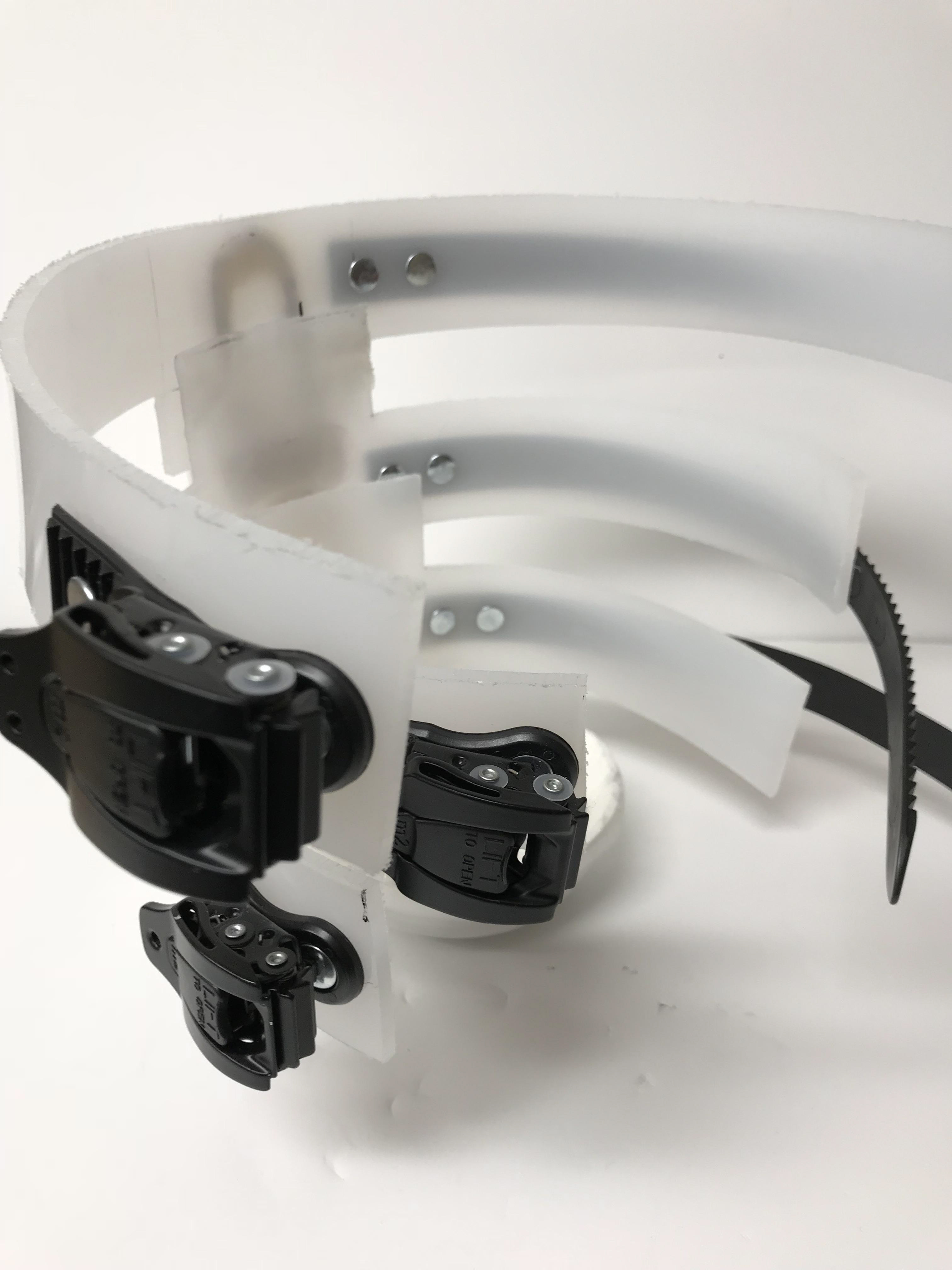
The issue with our first iteration was that since the adjustability is based on a backbone, causing the center of each section to misalign. Thus, we created a second iteration where the adjustability was based on the rigid cup area. The redesign process included a similar cardboard rapid prototyping and 3D printing. We also machined a usable prototype and are currently mechanical failure testing, We will be testing it at a gait lab. Due to patenting reasons, current progress cannot be fully documented.
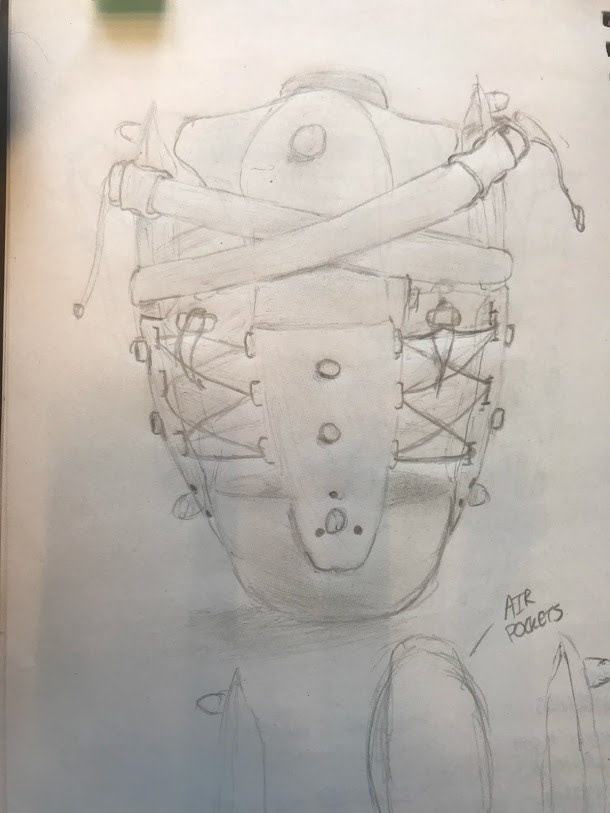
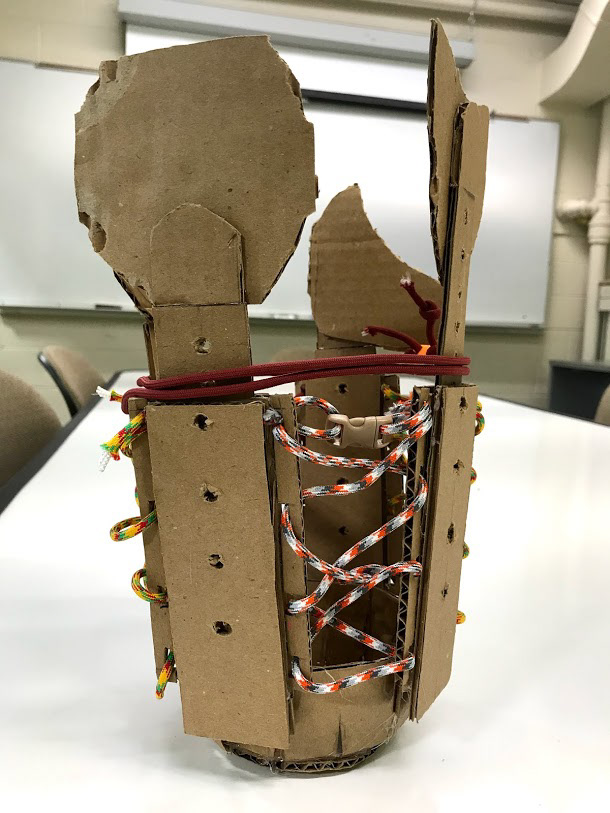
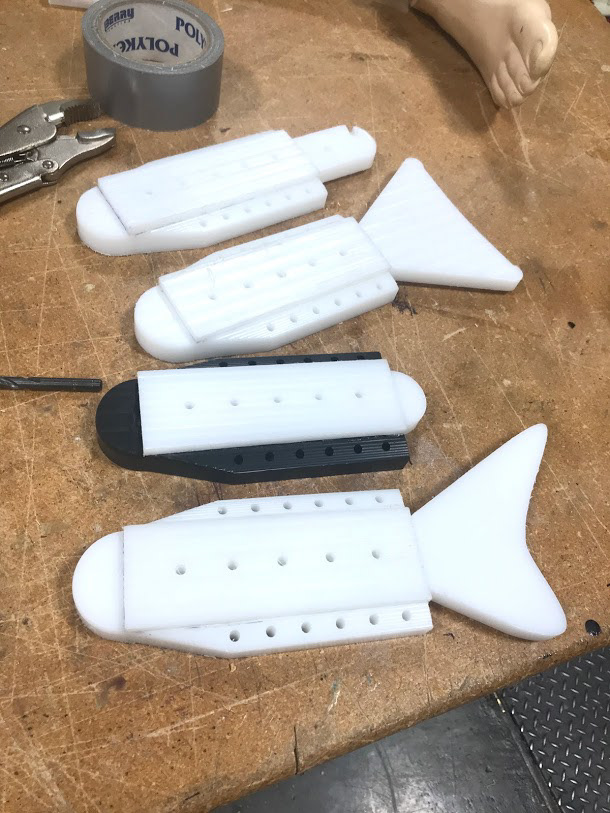