To create higher fidelity prosthetic models, we used a combination of 3D printing, in-house machining and heat molding. Most of the sockets we designed were for additive manufacturing, especially for injection molding. For our 3D prints, I designed the pieces using Onshape so that I could collaborate with my other team members. We created representative prototypes that we could run initial fitting tests on using residual limb molds. I used PLA printers so that we could quickly produce many different designs and test them together.
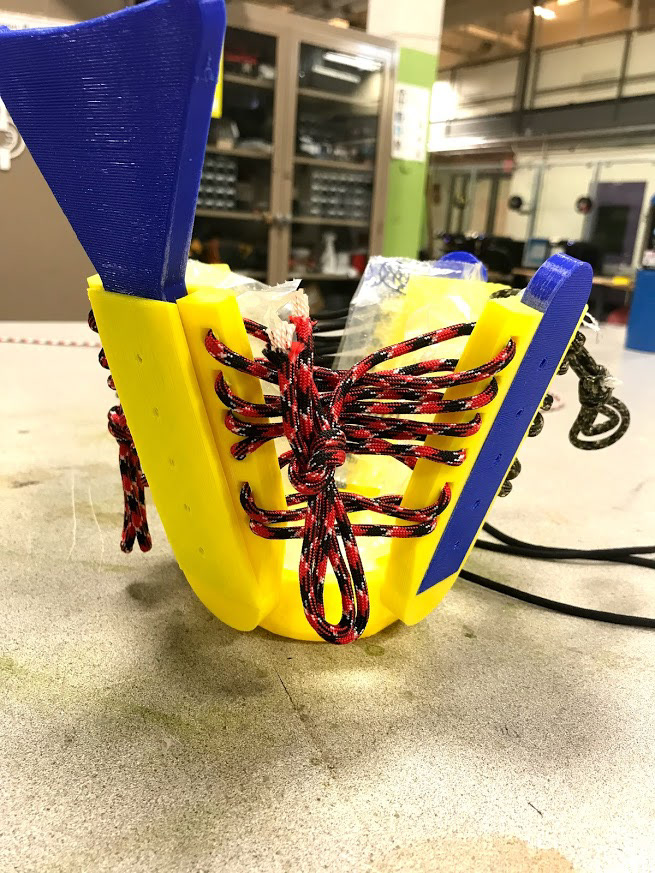
We used heat molding to create inner cushioning systems. We were playing with the use of air pockets to create a better, more comfortable fit with the outer socket shell. We wanted to create customized shapes so that they fit into our different designs. To do this, I used a torch to heat up metal screws, then pressed against two sheets of polyurethane into the desired shape. The two sheets fused under the concentrated heat and pressure.We then repurposed one-way valves to create inflatable air pockets.
We also used a form of heat molding to customize the shape of outer socket prototypes. I heated sections of LDPE using heat guns until it reached right under its melting point. LDPE has a low melting point and is soft so that it is easy for molding and prototyping. The LDPE turned translucent, which indicated it would hold the shape when cooled. I pressed the plastics around different molds to hold their shapes. We also used this same concept to fuse pieces of LDPE together. This was important for fusing the base piece to the main backbone (pictured below).
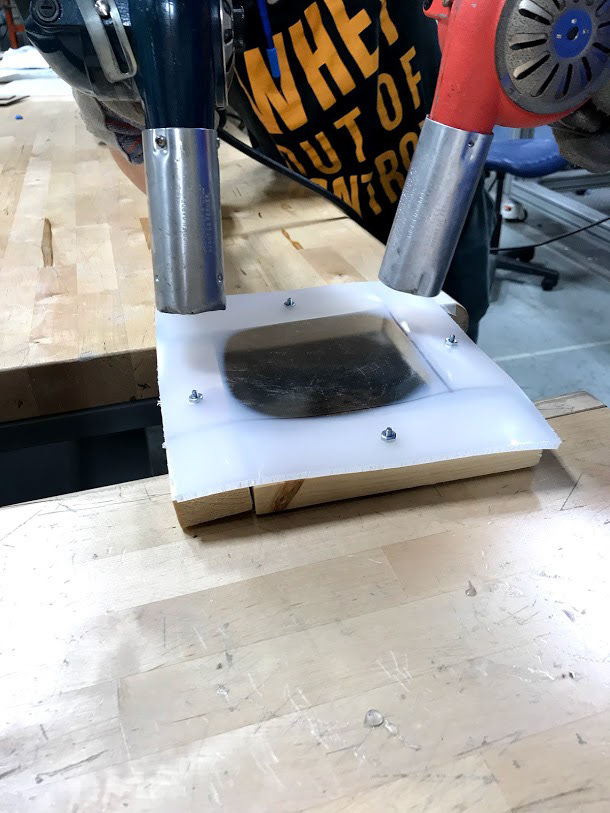
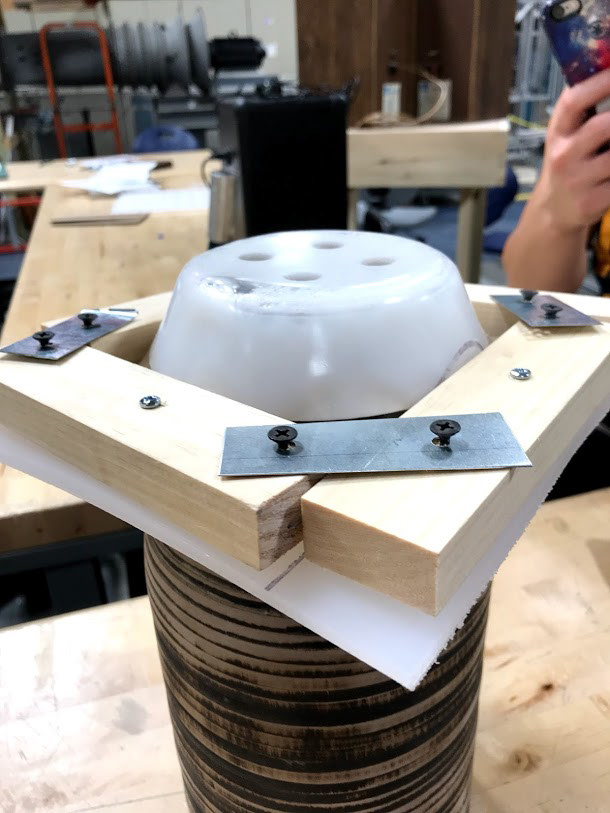
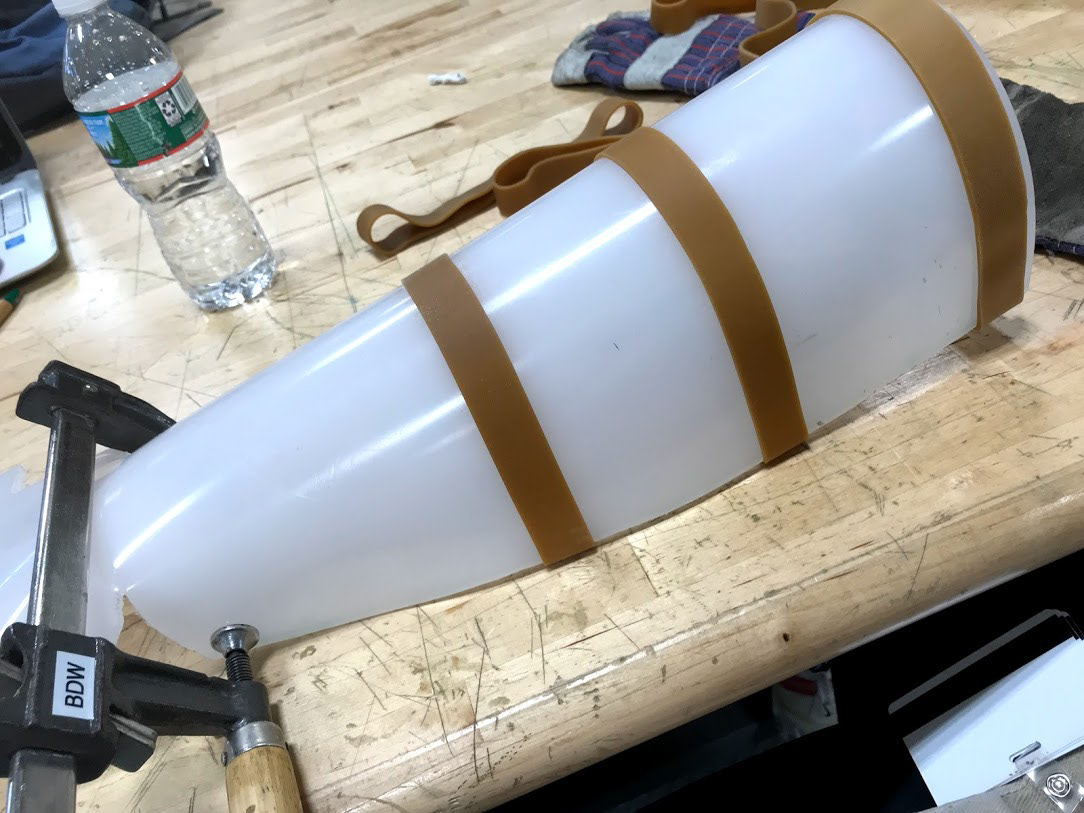
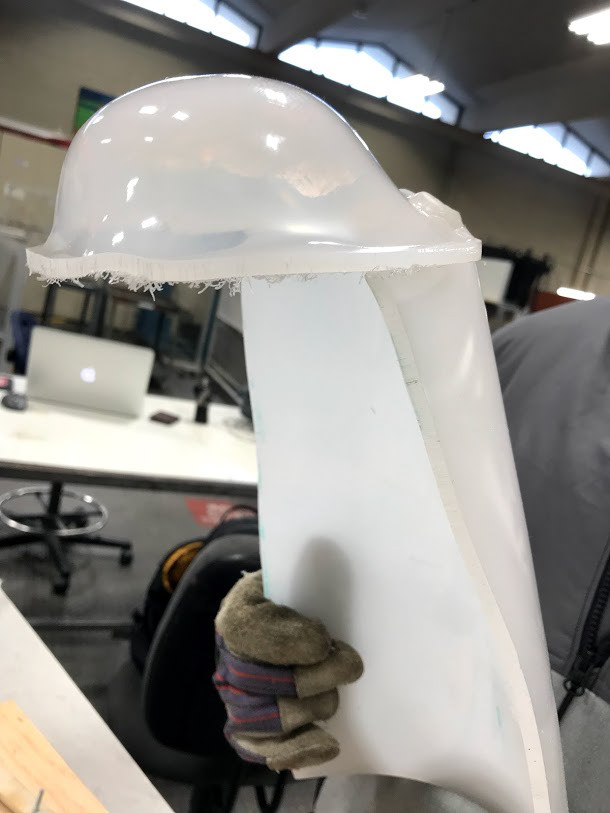
To create a more uniform heating and molding process, I retro-fitted a previous project to make a vacuum form machine. The machine already had a heating element and was used to heat thermoplastics. re-wired the circuitry so that it would plug into our new wall plugs in my university's Design Workshop and added a new vacuum system. The intent was to use this for our new prosthetic prototypes, but I created a teaching module so that other students could be trained and use the vacuum form for their future projects.
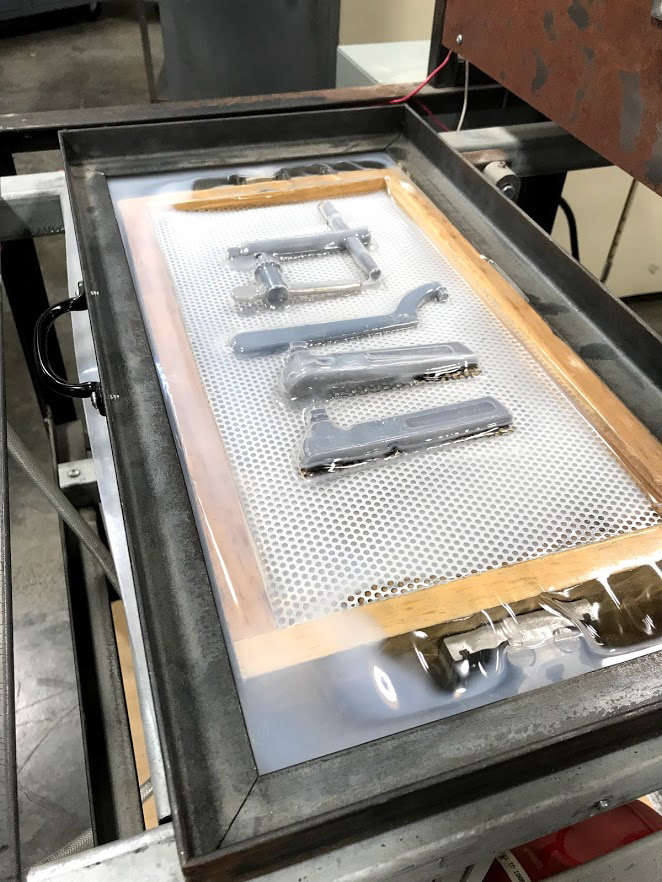