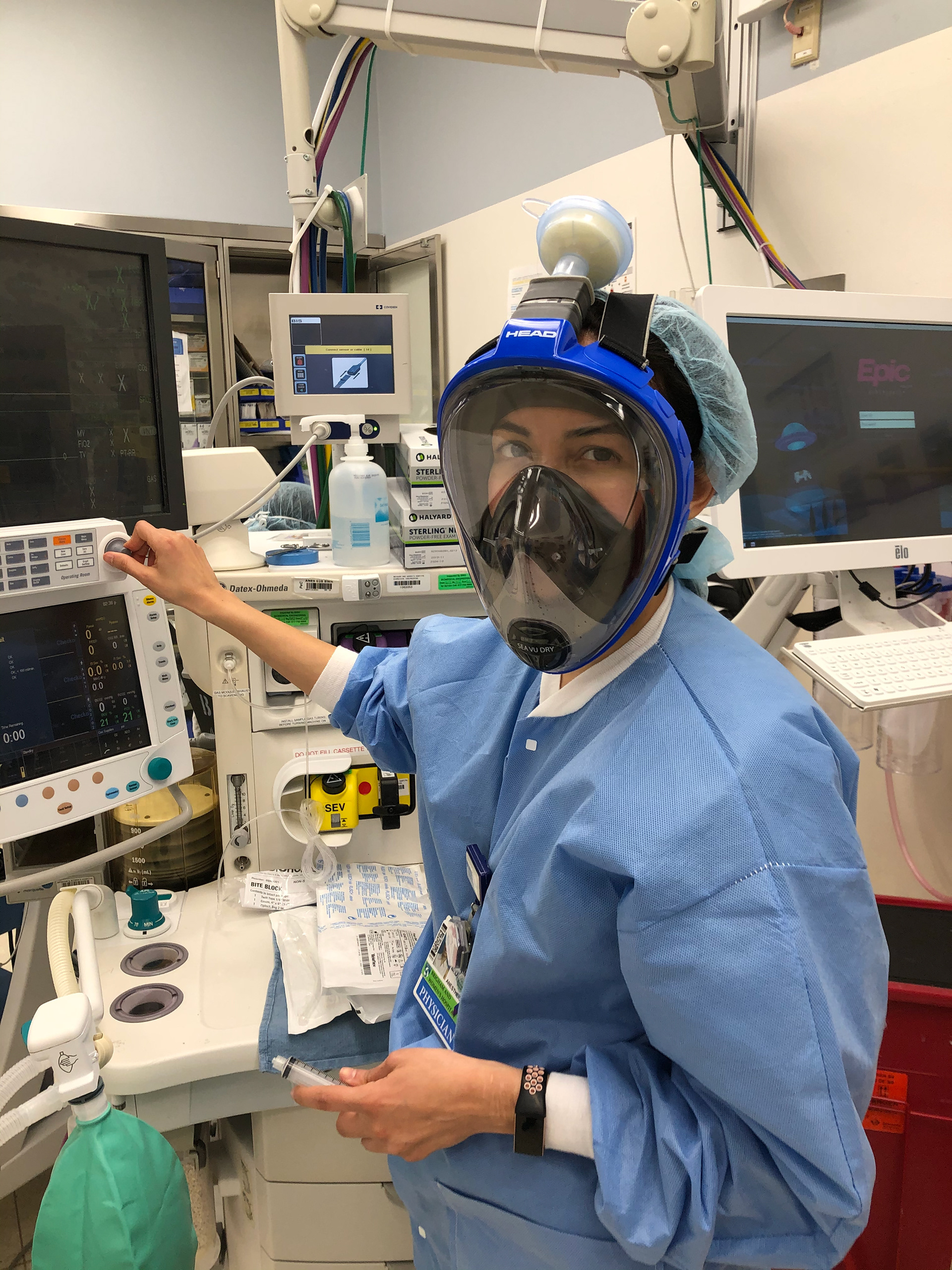
https://maskson.org/
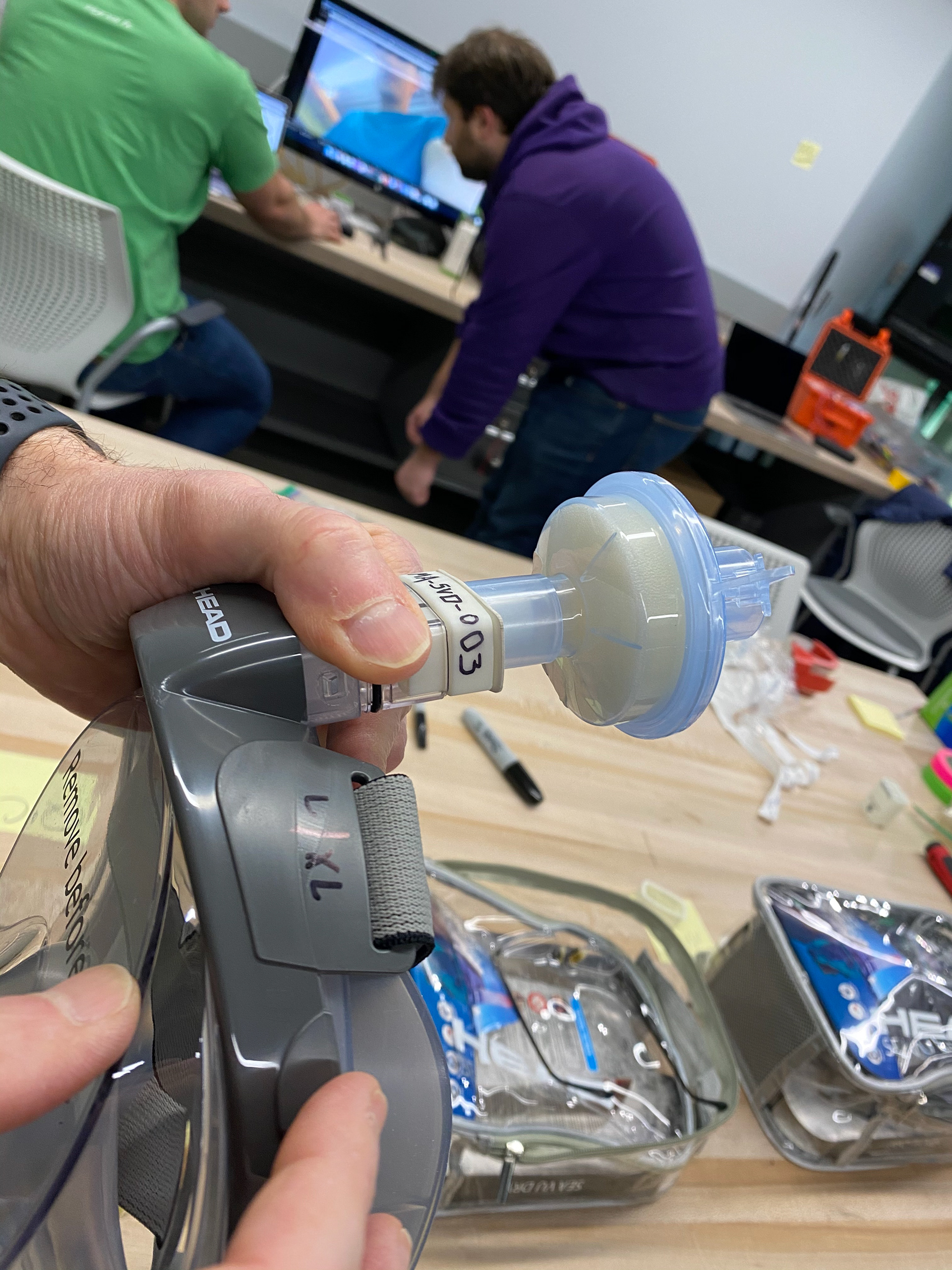
In March of 2020, the COVID-19 pandemic created a massive shortage of Personal Protective Equipment (PPE) all across the world. This shortage gravely affected healthcare workers, as they had to come up with ways to reuse old PPE; they had to put themselves at an even higher risk for contracting the virus.
Google engineers in Boston recognized the shortage and were thinking of ways to create a reusable PPE that could be used in this emergency situation that would sufficiently protect healthcare workers from the virus. They reached out to universities, hospitals and R&D companies (including my company, Onshape) around the Boston area who could help create an effective device and accelerate production. From here, MasksOn was formed.
I was a part of the original R&D team, working on prototyping and QA of our devices. With our team's research, we found that snorkel masks are highly effective in directing airflow through one opening (the snorkel). We also recognized that we could attach ventilator filters commonly used to purify hospital air from virus particles. Our main jobs were to 1) find an effective mask where we can force all intake and exhaust through the snorkel attachment, 2) Find an effective ventilator filter that would filter COVID-19 ,3) Create an air-tight durable adapter to connect the filter to the snorkel mask while being comfortable to breathe through, 4) Create a production process for efficient production line creation, 5) Create a cleaning process for healthcare workers to follow and 6) Get FDA emergency-use approval
Choosing snorkel mask: We first researched different types of full -faced snorkel masks. We needed a base that we could divert all exhaust through the snorkel so that there are no air openings around the user's mouth. We decided to use the HEAD Sea Vu dry mask, as it had an exhaust in the front and in the snorkel; using surgical plastic and re-adjusting the front exhaust, we could divert all exhale air up through the snorkel. As a result, we could control all airflow through the filter so that there is no chance of viral exposure.
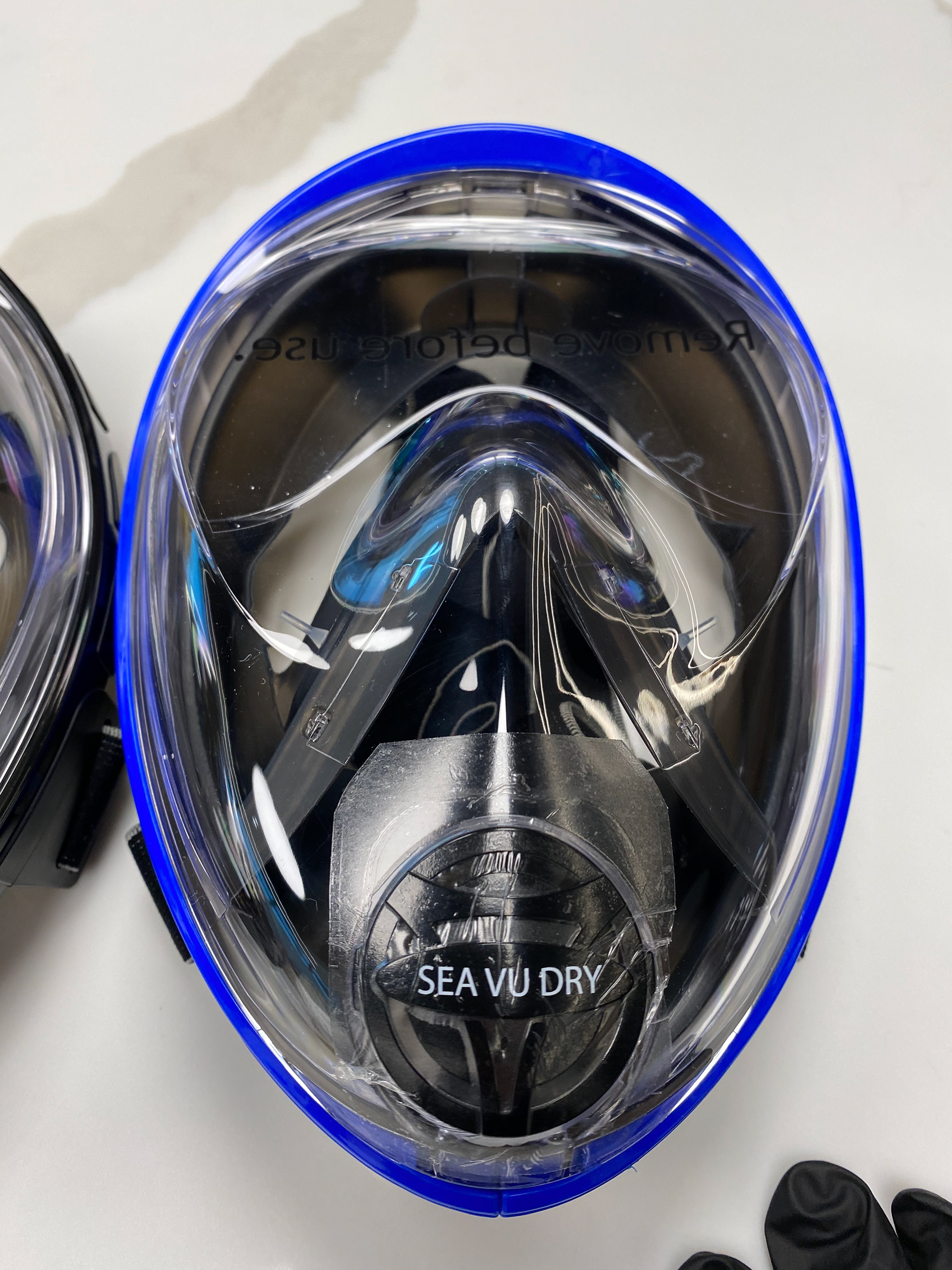
Adjustments to exhausts to force all intake and outtake through the snorkel
Determining filter: N95 masks are the standard PPE that is proven to filter out COVID-19 virus. We wanted to use a filter that will filter out the COVID virus and are commonly found in healthcare settings. Ideally, the users could also reuse these filters. That way, the user can easily replace filters after multiple uses once they run out of the ones we provide. We chose to use HMEF and Bacterial/ Viral filters because they are affective against the virus and are readily available. They also have universal attachments that would work with our masks and other medical airflow devices.
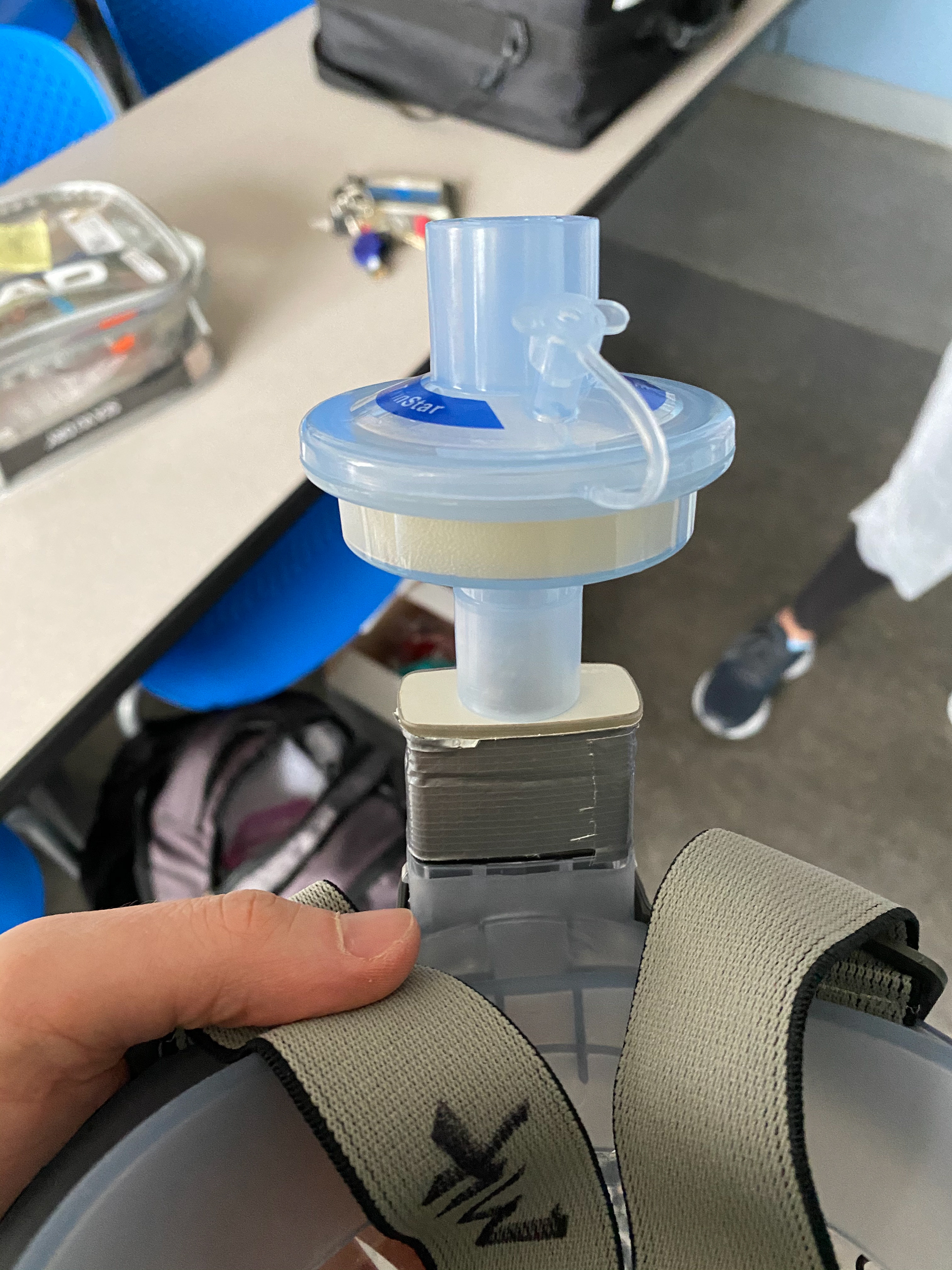
Creating Adapters: We had to design and prototype adapters from scratch. We (Onshape) had partnered with other design and manufacturing companies to quickly iterate and test prototypes. We would design the model on Onshape, run simulations and testing, print with Formlabs, New Balance and other tech companies in the Boston area, then test our prototypes with biotech companies and local universities. Our first design had one intake through the filter, then two one-way exhausts:
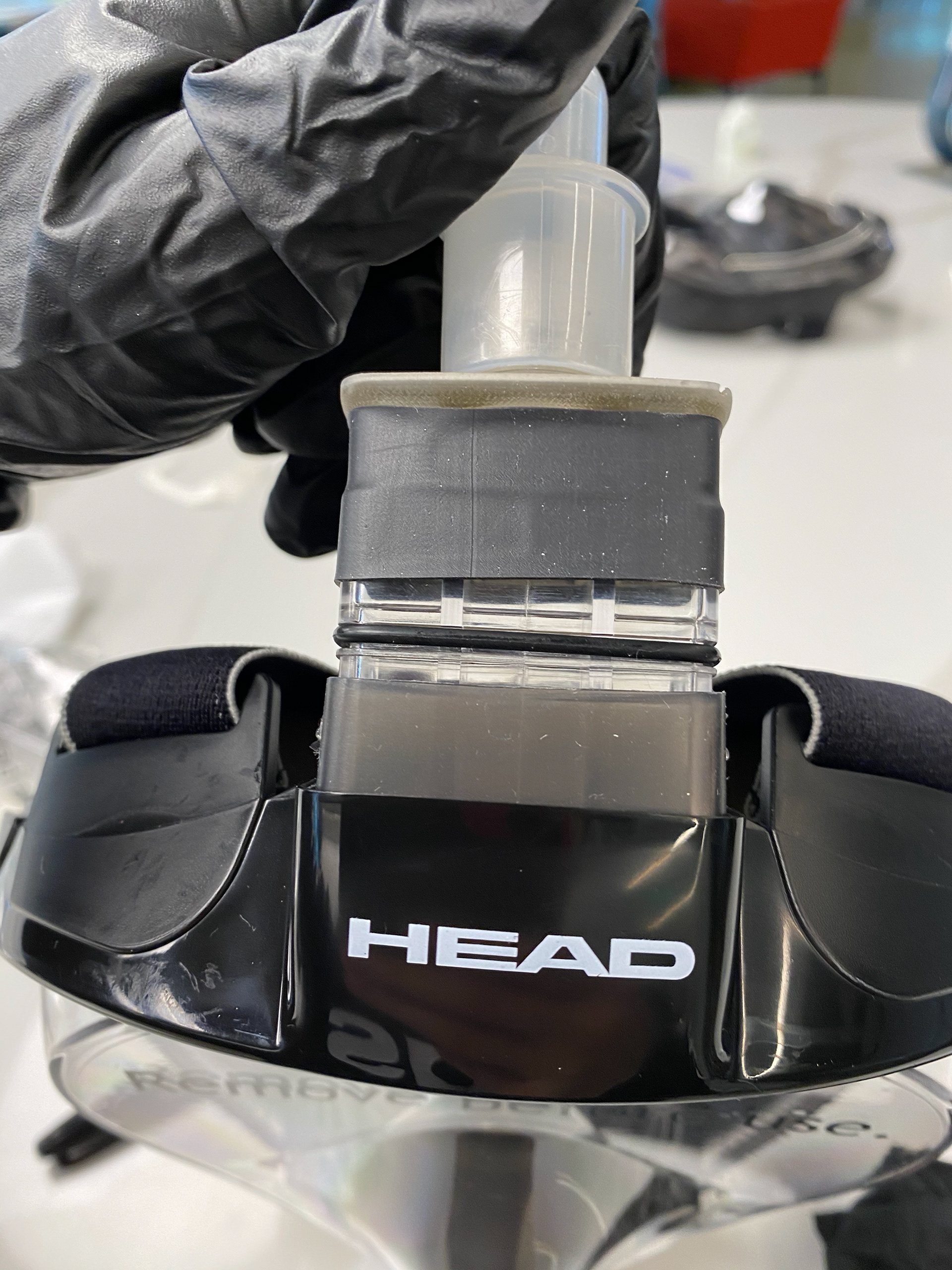
Our first prototype
This design allowed for easier breathing, as the user could exhale normally without any resistance. The adapter used patient-safe dental plastic so that it would not deteriorate under constant cyclic stress. We used a flexible polymer flap that would return to a closed shape after breathing, then sealed our attachment using a medical- graded heat shrink. I ran standard test procedures for PPE to see how effective the adapter was in sealing off extraneous airflow and in common working conditions.
Through these prototype tests, we recognized that the flap could get stuck in the open position, which is something we could not allow. It forced us to redesign the adapter so that all airflow goes through our attached filter. Breathing was a bit more difficult, but was really safe. The second filter design within our full mask passed FDA emergency use approval
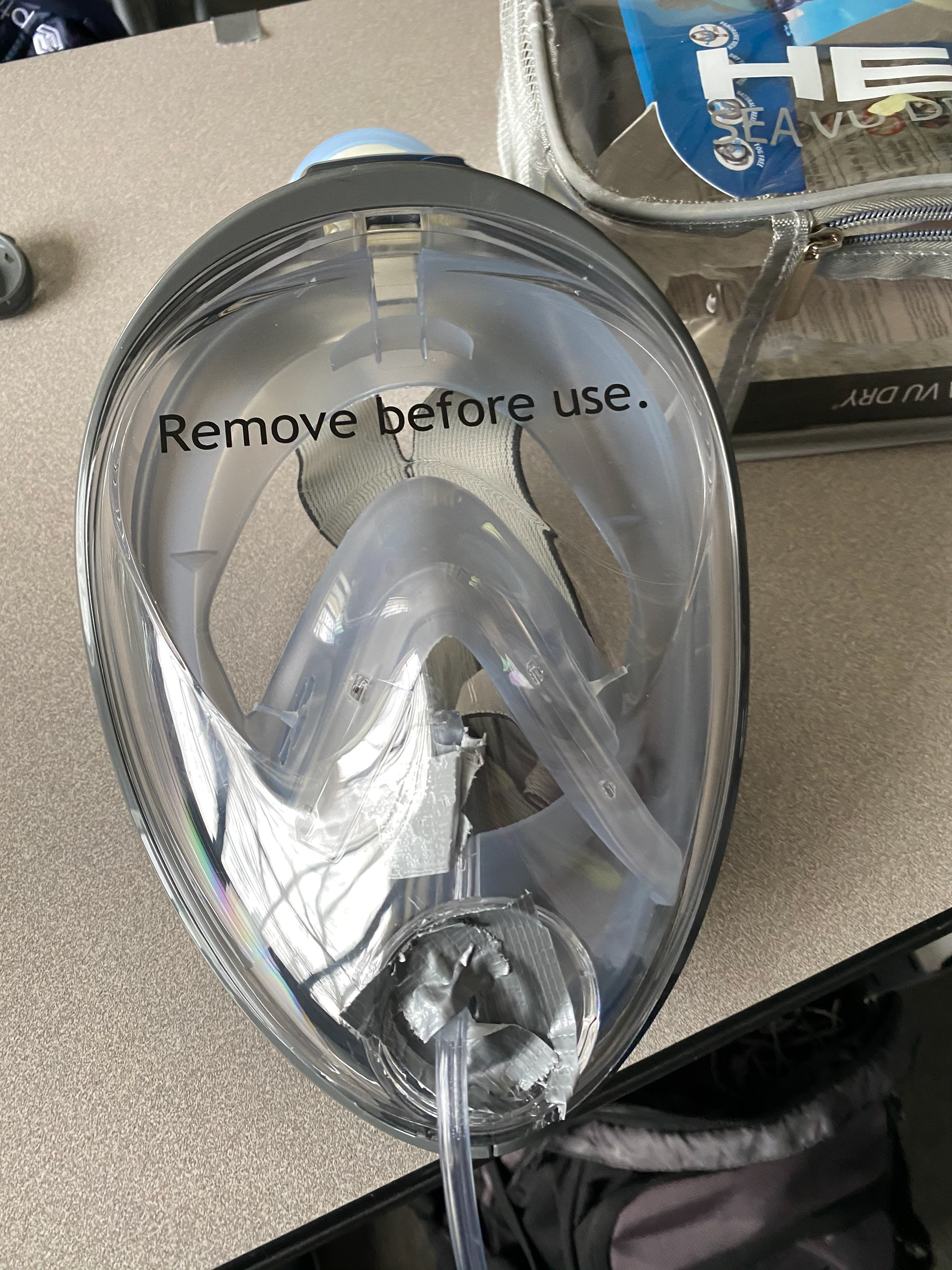
One test to determine the seal created in the mask
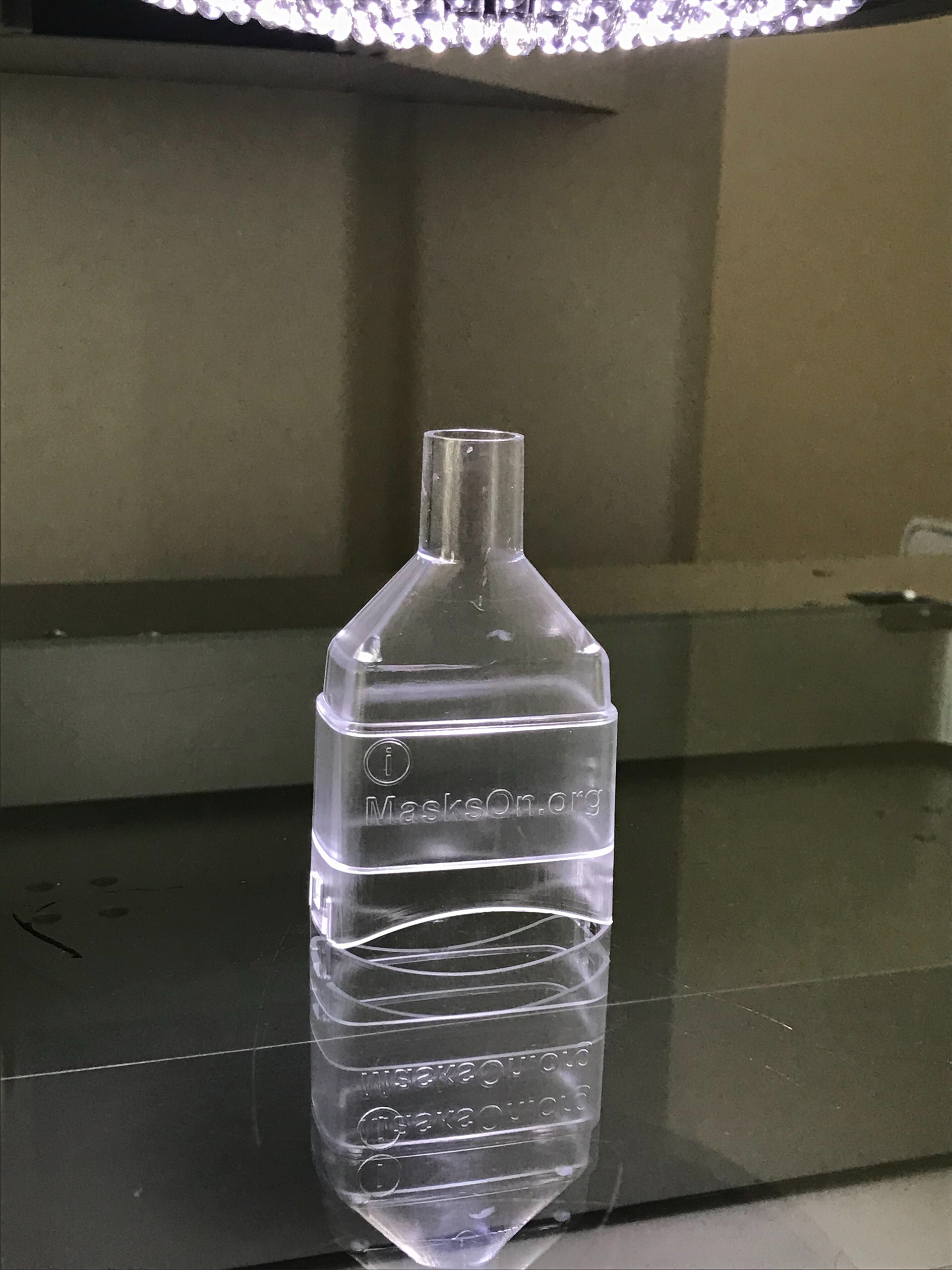
Second iteration: all airflow through the HMEF filter
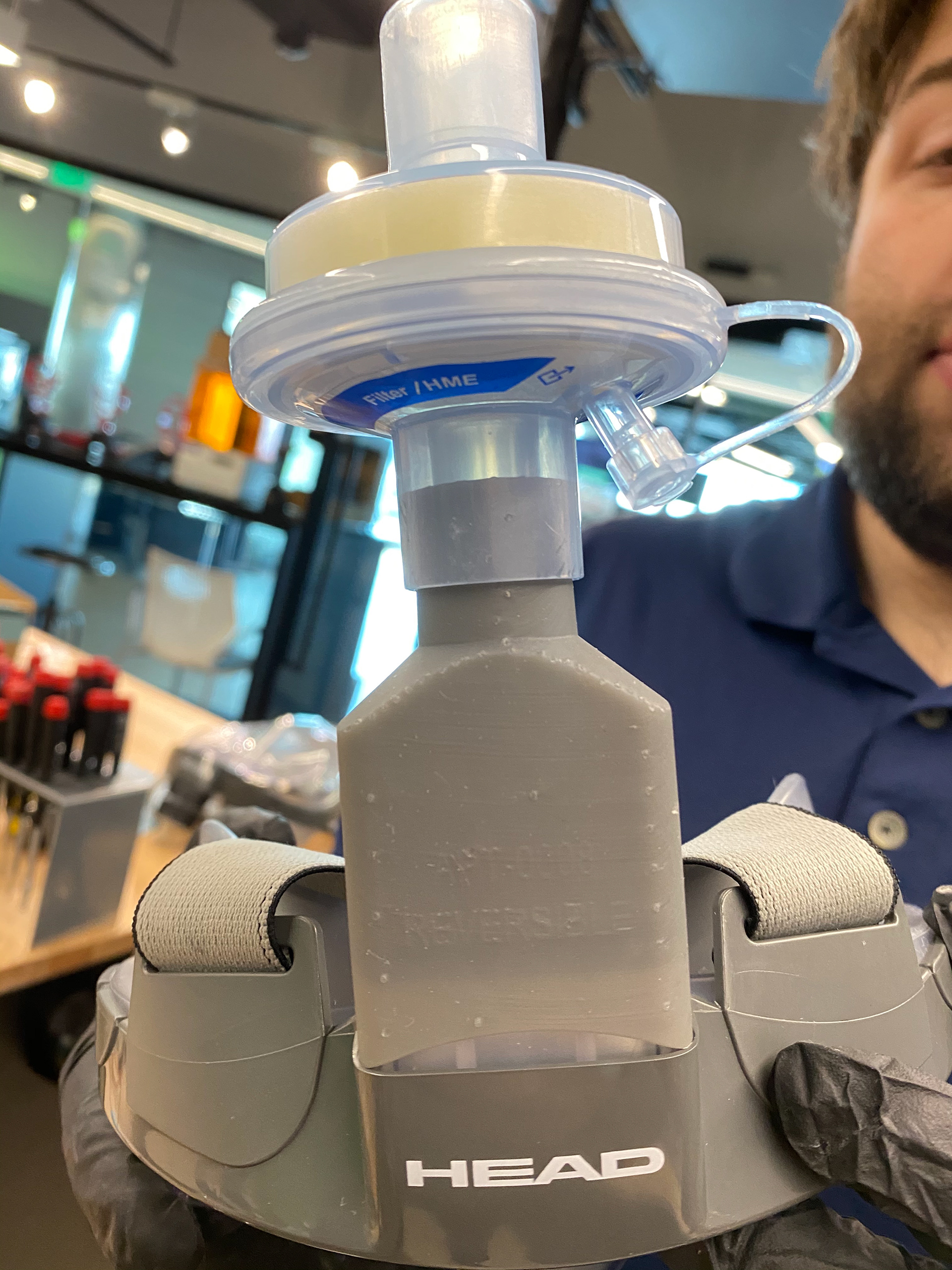
Production process: As we were prototyping our mask designs, we also put together manufacturing processes for our PPE kits. I was in charge of ramping up production and designing QA tests. We first started by recruiting volunteers and working out of PTC's offices:
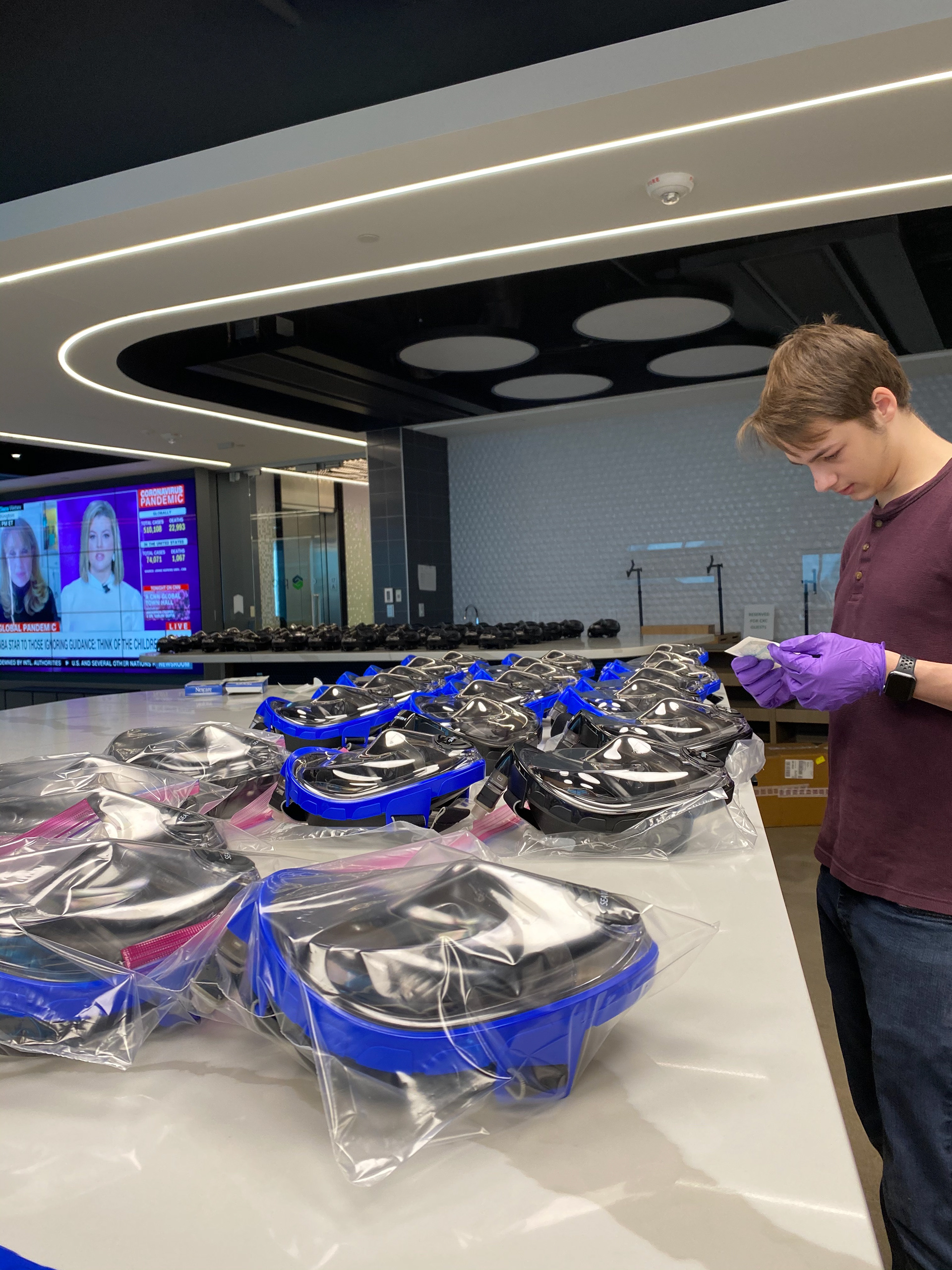
With volunteers, we could figure out pain points in our production system while finalizing our instruction manuals. With this setup, we could ship out roughly 500 a day; however, demand was much higher than we could produce during the first months of the pandemic. Once we streamlined our production and ramped up, we hired an outside production company to take over our large scale production, allowing us to ship out 2000+ a day to healthcare facilities all over the world:
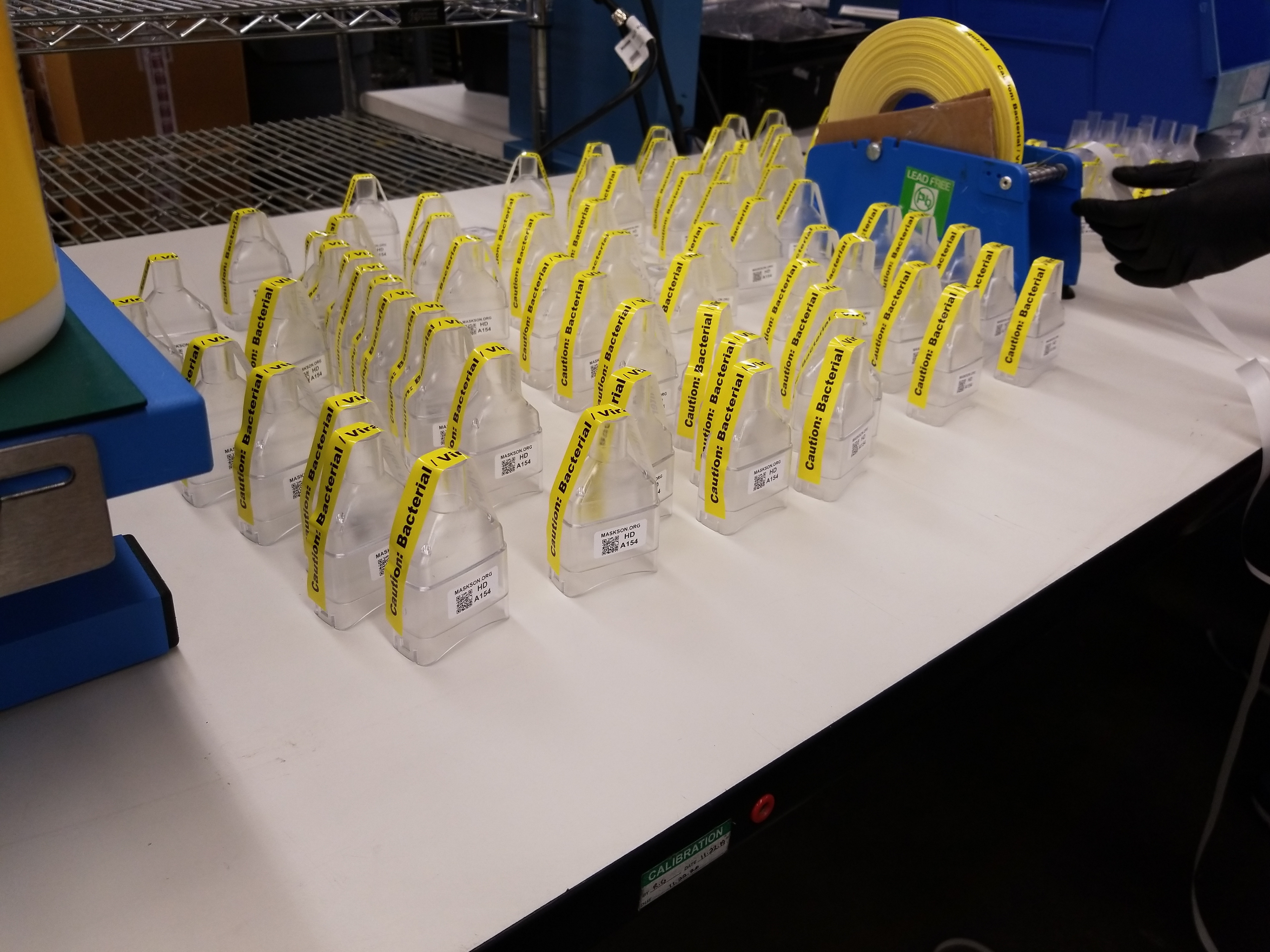
Lightspeed manufacturing prepping PPE kits for shipping
With the amount of collaboration between renown companies in the Boston area, we shipped out effective, safe, alternative PPE with FDA Emergency Use Approval in a little over a month. We were also able to turn this initiative from a side project to a full non-profit organization that was highlighted by GoFundMe. Our goal was to provide healthcare facilities access to PPE when traditional PPE is not available. We are still shipping masks to areas that need alternative PPE. For more information, please visit MasksOn.org